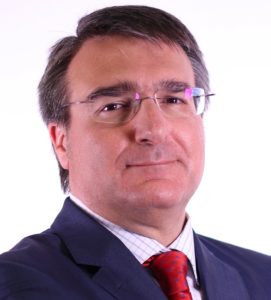
José Andrés López de Fez. Ingeniero industrial
La cuarta revolución industrial es una realidad innegable, estrechamente vinculada con internet. A diferencia de las revoluciones anteriores, ésta no cambia lo que estamos haciendo, sino que nos cambia a nosotros, a las personas. Los gemelos digitales son la síntesis de todas las tecnologías asociadas a esta revolución y están cambiando la forma en que trabajamos y nos relacionamos. Ya nada será como antes. ¿Estás preparad@ para el presente?
La cuarta revolución industrial es una especie de tormenta perfecta, pero en sentido positivo, que se basa en la convergencia simultánea en términos de coste asequible de tecnologías que ya estaban previamente exploradas, pero a un nivel de coste difícilmente asumible por la mayoría de las empresas.
Así, la inteligencia artificial se basa en desarrollos matemáticos que se conocen desde los años 80 del siglo pasado (si no antes), pero que precisaban de una capacidad de cálculo que hasta ahora no ha estado disponible a un coste razonable.
La disminución de costes ha hecho asimismo posible la popularización en el empleo de sensores (inter) conectados y con capacidad de transmitir la información capturada a través de internet, más allá de las fronteras del propio entorno fabril. Son los sensores IIoT que proporcionan datos e información, combinada o no con algoritmos de inteligencia artificial, que permiten hacer realidad el viejo sueño del mantenimiento predictivo. Una vez más, un viejo concepto ya conocido, pero que no había podido desplegarse masivamente por falta de una capacidad de cálculo que le diera soporte.
A nivel de simulación, la capacidad de computación a coste razonable también está permitiendo el abordaje de problemas tipo “What-if”, multiplicando el número de grados de libertad en los procesos simulados sin penalizar la rapidez en la obtención de resultados. De esta manera, los diseños son mucho más fiables en un menor espacio de tiempo, lo que redunda en un menor time-to-market.
Como vemos, la cuarta revolución industrial gira en torno al concepto de dato. Dato que aporta por sí mismo información o que permite inferir información en base a algoritmos más o menos complicados. Es esa orientación al dato lo que hace posible la trazabilidad de la información a lo largo de todo el ciclo de vida de los bienes producidos, así como de los servicios prestados.
Esos datos pueden tener origen en el mundo real físico o en el mundo virtual del diseño. Pero requieren ser conectados para poder analizar en tiempo real el impacto de los valores reales que capturan los sensores y compararlos con las condiciones de diseño. En muchas ocasiones, la rapidez de esa comunicación no es relevante, pero en otras es crítica. Es ahí donde hace aparición las comunicaciones móviles 5G, con casi nula latencia, y que permiten una sincronización de máquinas y procesos como antes no era posible.
Pero toda oportunidad tiene su riesgo. En el caso de la cuarta revolución industrial, el riesgo se llama ciberseguridad. Sin ciberseguridad, no es posible la industria 4.0. Es como dejar abiertas de par en par las puertas de tu casa con la esperanza de que no entre ningún ladrón. Inviable. Por eso, toda prevención en términos de ciberseguridad es poca. Si no puedes evitar que te ataquen, por lo menos pónselo complicado al atacante.
Así pues, la cuarta revolución industrial descansa sobre varios pilares (inteligencia artificial, simulación, IIoT, computación en la nube, impresión 3 D, 5G, etc) que gestionan cantidades ingentes de datos de todo tipo (video, audio, fotografías, texto…)
Hay un último aspecto que no he mencionado, y no por ello menor, y que es de vital importancia: las personas. Esta es, sin duda, una revolución tecnológica. Pero, a diferencia de las otras, ésta no cambia lo que estamos haciendo, sino que nos cambia a nosotros. Y a la forma en que trabajamos y nos relacionamos. Y una de esas formas se refiere a las representaciones abstractas del mundo físico. Conceptos como gemelo digital o metaverso serán cada vez más comunes, aunque el primero está mucho más avanzado que el segundo.
Todas las tecnologías anteriormente mencionadas participan en el concepto de gemelo digital (GD). Pero, ¿qué es exactamente un GD? ¿En qué se parecen y en qué se diferencian el diseño asistido por ordenador (CAD) y la tecnología del GD?
Ambas tecnologías abordan la representación abstracta de un objeto real. Pero podríamos decir que un diseño asistido por ordenador es un subconjunto de los componentes de un gemelo digital.
Así, en esa abstracción de la realidad, lo más básico es la identificación de las dimensiones del objeto y de sus componentes, ya sea en 2D o en 3D, de sus tolerancias, de los tratamientos superficiales y térmicos que pudieran ser necesarios para la fabricación de dichas partes, las normas industriales aplicables, etc. En definitiva, la identificación de todos aquellos atributos necesarios para la fabricación de un objeto y sus partes. Eso sería un CAD.
Pero eso es sólo una parte de la representación del objeto. Lo normal es que ese objeto esté sujeto a solicitaciones mecánicas, a movimientos, a aceleraciones y, en general, a todo tipo de fuerzas que producen desgaste, fatiga, aumento de temperatura, etc. que hay que simular y ver su impacto en el funcionamiento del objeto a lo largo de su ciclo de vida.
Ese objeto se ha fabricado a partir de unas especificaciones. Hasta ahora, la única manera de verificar y validar que la documentación técnica desarrollada respondía a dichas especificaciones era mediante la fabricación de un prototipo de validación, un objeto físico. Ahora, sin embargo, si tuviéramos un modelo digital con todos los atributos estáticos y dinámicos de cada uno de sus componentes y modeladas las relaciones entre ellos, no sería necesario fabricar ese prototipo y se podría acometer una primera serie corta con un nivel de riesgo muy controlado (siempre habrá modelos incorrectos que introducen incertidumbre en el conjunto final).
Un gemelo digital puede ser desde un equipo, una persona y su interacción ergonómica, hasta toda la representación de una planta industrial. No es una representación o copia de algo, sino que es una interacción que va más allá, muestra comportamientos, procesa información, entrega datos que son determinantes para la validación de un proceso y permite iteraciones continuas de diseño para ser probado en el mundo virtual sin tener que detener la línea de producción para ver cómo se pueden hacer mejor.
Entonces, ¿una realidad física tiene un solo gemelo digital? En realidad, a día de hoy, lo más probable es que no. El mundo digital de hoy abarca un amplio espectro de tecnologías y necesidades del mercado, por lo que ha habido muchas interpretaciones del concepto de gemelo digital.
Quizás la mejor definición sea la de “Representaciones digitales dinámicas que permiten a las empresas optimizar el rendimiento de sus activos, procesos y negocios “.
Podemos definir 3 niveles de gemelos digitales, cada uno con diferentes subniveles, y que forman un ecosistema integrado:
Es decir: en general, hablamos de un ecosistema de gemelos digitales asociados a una realidad física, cada uno especializado en una faceta de dicha realidad e conectados entre sí. La tecnología del nivel 3 está todavía en pañales y no nos referiremos a ella en lo que sigue. Baste decir que las versiones modernas de los ERP y los BPMs son herramientas claves en dicho nivel como orquestadores de procesos.
En el nivel 1, o de activo, tenemos los gemelos digitales de diseño. Son una extensión de los conocidos sistemas CAD/CAE y de los PLM, y se enfocan en optimizar el ciclo de vida a nivel diseño y fabricación de los activos más complejos
Este gemelo digital captura datos la ingeniería de detalle para visualizar, simular y analizar funciones de los activos. Así mismo, es capaz de capturar datos de rendimiento en una amplia variedad de operaciones y entornos, ayudando a cerrar el ciclo de diseño mediante la monitorización de rendimientos, la detección de problemas y la identificación de mejoras, tanto para el producto como para su propia fabricación.
Pueden agregar mucho más valor en situaciones donde se despliegan múltiples unidades de activos a través de diferentes geografías y/o condiciones de operación, pues permiten recabar incluso información de detalle sobre los activos para obtener reducciones de coste, incluyendo una organización y una planificación más efectiva más efectiva de los recursos a desplegar durante la operación y el mantenimiento:
- Imitando la funcionalidad de los productos y activos existentes
- Capturando y visualizando información de sensores en tiempo real
- Obteniendo una mejor comprensión del producto / características de la interfaz de la máquina
- Usando los datos para mejorar el diseño
En el nivel 2 tenemos los gemelos digitales de proceso. Son la base de los sistemas de gestión de rendimiento de activos (APM), y pueden ser de tres tipos en función de sus capacidades:
- Con capacidades de supervisión
- Con capacidades de diagnóstico y control
- Con capacidades predictivas
Los gemelos digitales de supervisión podemos considerarlos como una evolución de los sistemas SCADA. Imitan la ejecución de procesos de la vida real, ya sea a nivel operativo o comercial y, en su forma más básica, ofrecen emulación visual (o animación) para ayudar al operador a comprender las características operativas estáticas o dinámicas del equipo, y cómo se relacionan con los resultados de sus prestaciones.
Pueden ayudar a:
- garantizar un funcionamiento coherente y estándares continuos
- planificar y probar el impacto de escenarios críticos
- probar visualmente nuevos modelos de proceso a nivel conceptual
Los gemelos digitales de diagnóstico y control brindan capacidades de diagnóstico dinámico, lo que permite analizar el rendimiento del proceso de extremo a extremo en tiempo real. Pueden ofrecer resultados impresionantes al apoyar la optimización del rendimiento de los activos y procesos del mundo real.
Vinculan los datos de sensores del mundo físico a los algoritmos analíticos y de minería de datos, proporcionando información detallada, precisa y procesable. Pueden activar alertas para solicitar una supervisión más cercana, diagnosticar problemas e identificar mejoras de rendimiento. También pueden vincular activos físicos y sistemas de control para que puedan ajustar automáticamente los parámetros del proceso a través de un bucle de actuación.
En definitiva, pueden ejecutar planes operativos de manera más efectiva. También pueden aumentar la productividad, mejorar el control e impulsar un rendimiento operativo más estable y confiable.
Por último, los gemelos digitales de proceso en su vertiente predictiva van un paso más allá e identifican oportunidades a partir del uso de datos del estado actual, para mejorar el rendimiento de los activos y de los procesos operativos.
Básicamente, son software de simulación predictiva y se pueden utilizar para evaluar escenarios futuros. Ayudan a los responsables de la toma de decisiones, probando y mostrando el impacto de diferentes escenarios, identificando oportunidades y riesgos sin incurrir en ningún coste.
Pueden responder a preguntas como «¿Qué pasa si?», «¿Qué es lo mejor?» y “¿Cómo lo hacemos?” utilizando modelos dinámicos de procesos comerciales y operativos reales. En definitiva, pueden verse como una gamificación de la toma de decisiones estratégicas a corto, medio y largo plazo.